Design and Control of Non-Linear Series Elastic Actuator (SEA) - Cable Drive
Published:
External Links:
- Published MS Thesis Non-linear series elastic cable drive actuator: Design and Controls
- Unidirectional Actuator with Customizable Series Elasticity, US Patent 18/911616 (pending)
- Prototype Video
- Code - GitHub Latest version for Moteus motor controller
Unidirectional cable-drive actuators are excellent for applications requiring high force with minimal resistance to back-driving. However, they face challenges when it comes to precise force control, especially in low-force regions.
This happens because high-torque motors struggle with rotor inertia, which reduces their sensitivity to small force changes. For wearable robotics, there’s also an added issue: sudden jerks when transitioning between Slack and Taut cable states.
A Promising Solution: Series Elastic Actuator (SEA)
One promising solution is a Series Elastic Actuator (SEA). By adding a spring element in series with the transmission, we can dampen the jerks and simplify low-force tracking by converting it into a position control problem.
However, traditional SEAs often fall short due to the reliance on linear springs, which create a trade-off:
- A soft spring is good for low forces but limits the actuator’s overall force capacity.
- A stiff spring allows high-force applications but sacrifices low-force sensitivity.
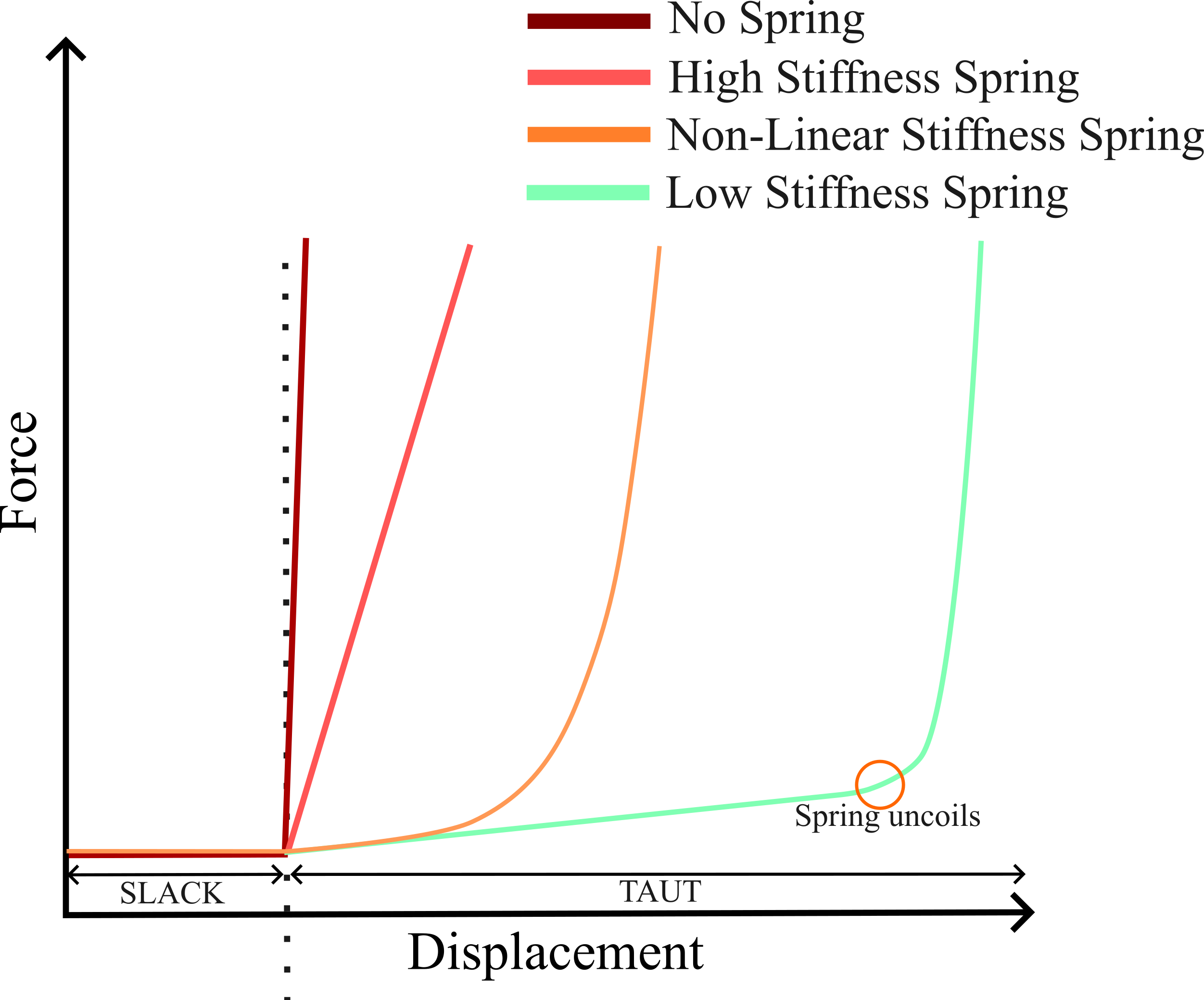

This project solves these issues with a non-linear Differential Elastic Actuator (refer) using a Cam-based spring mechanism. The Cam enables mechanical programming of the stiffness, making it adaptable for different needs.
At low forces, the actuator acts like a soft spring, maintaining tension to avoid slack. As forces increase, the stiffness gradually ramps up, eventually disengaging the spring to behave like a traditional cable-driven system.
Key Benefits:
- Achieves both high-force capability and excellent low-force sensitivity.
- The CAM-based mechanism is tunable for diverse applications, such as delicate handling (e.g., picking a strawberry) and lifting heavy objects.
Design and Prototype
The actuator combines a CAM-based spring mechanism with a kinematic pulley arrangement to achieve a tailored stiffness profile. The reasoning for pulley configuration is based off the need to have very-low stiffness requiring large deflections. Further, adjustments to the CAM shape and pulley configuration enable customization for specific applications. Thus, allowing user to mechanically program the non-linear stiffness curve for various applications. This current design was optimized for use with an ankle exoskeleton, where a near zero stiffness is desired during swing phase of walking and high stiffness during stance phase, with a smooth transition in between.
Key Features:
- Two Force Modes:
- Low-force mode: The spring is engaged, providing very low stiffness to maintain tension even with large deflections.
- High-force mode: The spring disengages, and the actuator functions as a traditional cable-driven system.
- Customizable Force-Displacement Curve:
- The force-displacement relationship can be fine-tuned for specific tasks, balancing low-force control and applying high-force values.
Hardware Used
- Motor: CubeMars AKE60-8
- Motor Controller: Odrive Pro, Transitioning to Moteus for its open-source firmware
- Compute: Jetson Nano Orin, supporting ML-based controllers for exoskeleton application
- Sensors: Two Encoders, MA600, one for the CAM Angle and another for the motor shaft and an IMU BNO085 for application with exoskeleton (Currently adding IMU support to Moteus firmware).
Controller Design
The actuator features broadly 2 control behavior - low-force and high-force modes, which are controlled by finite state-machine architecture, with different control strategies for each:
Low-Force Mode: Cascaded PD controller with gains fine-tuned for fast response and disturbance rejection. The loop is closed around cam angle error for which PD controller outputs the velocity command which is tracked by low-level controller within motor-controller.
High-Force Mode: In high-force region, the current feedback in motor is sufficient to accurately track the cable force values / motor torque. Thus, internal low-level controller works well for stability in high-force mode.
Transition: For transition between the two regions low-level velocity controller is used with ramped velocity trajectory to avoid abrupt changes.
This hybrid strategy ensures precise force tracking across the actuator’s entire operating range 1-200N.
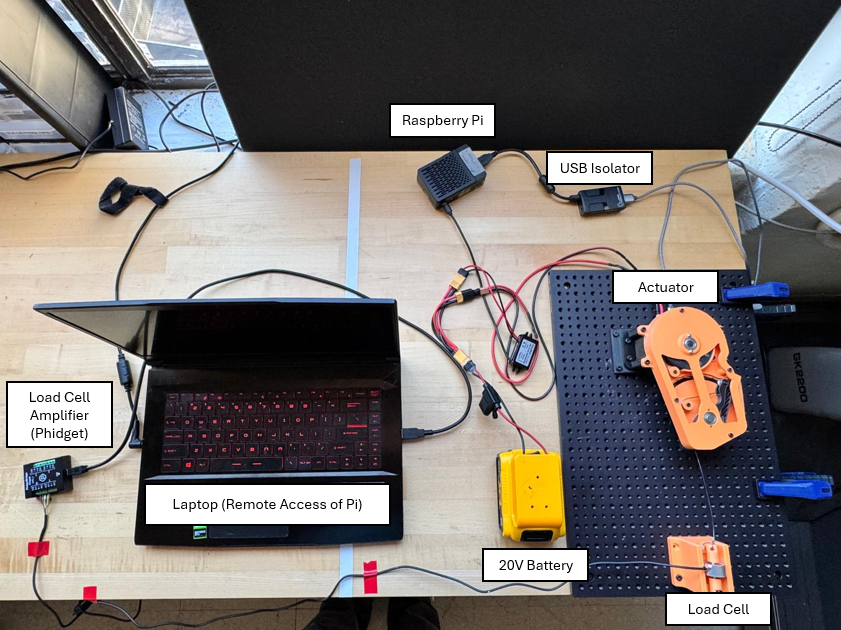
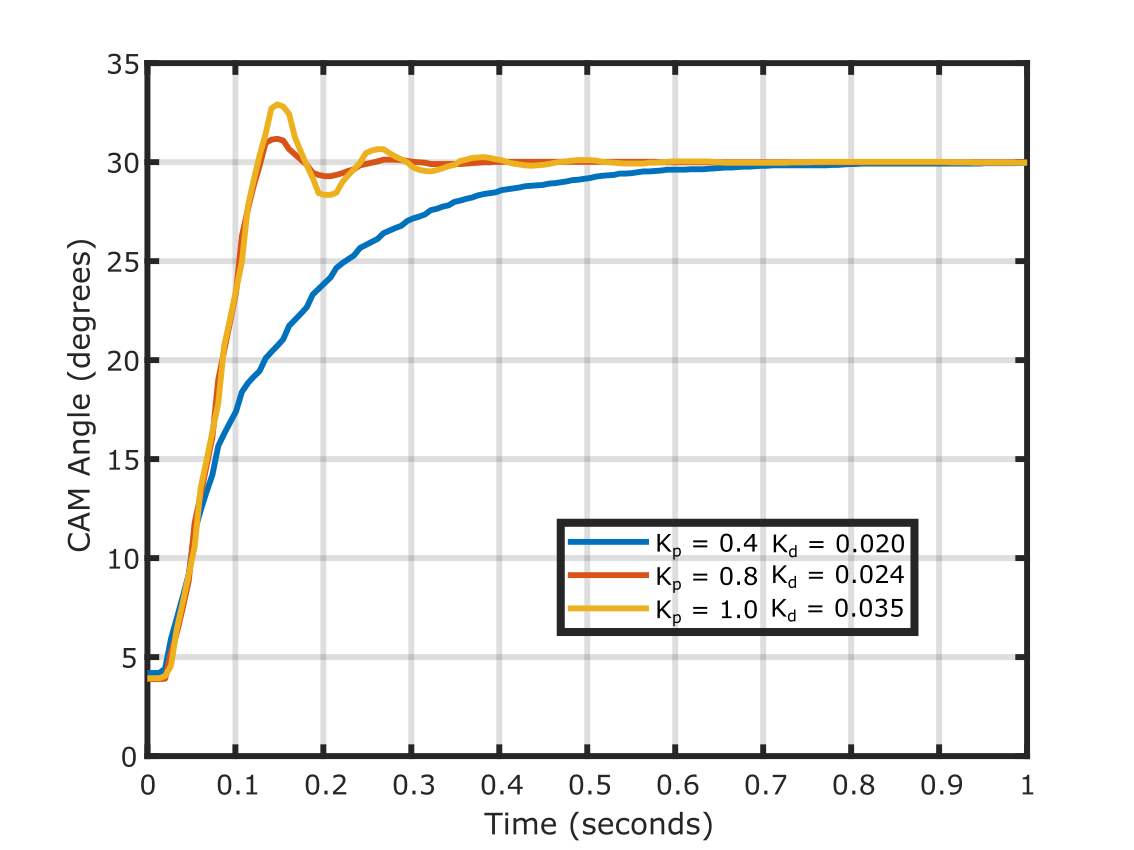
This innovative SEA design bridges the gap between low-force sensitivity and high-force capability, making it a versatile solution for applications ranging from wearable robotics to industrial grippers.